冬奥火炬研发技术负责人黄翔宇:
“飞扬”火炬是怎样炼成的

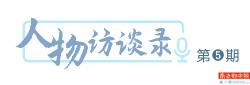
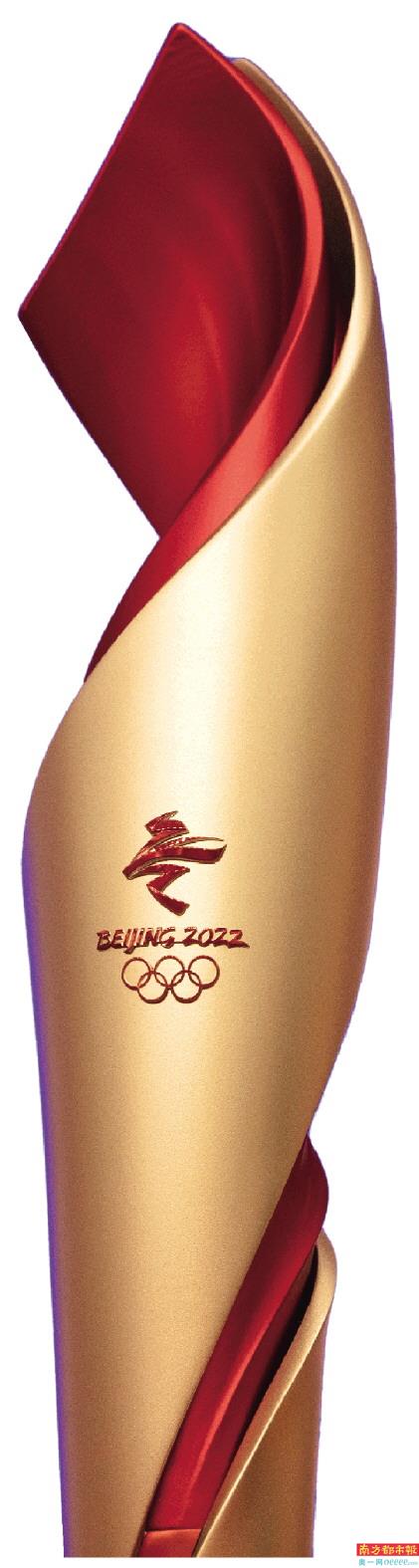
北京冬奥会“飞扬”火炬。 新华社发

人物名片
黄翔宇 上海石化副总经理、火炬量产项目领导小组副组长,冬奥火炬研制任务技术攻关团队负责人。
北京冬奥会“飞扬”火炬外形亮丽,技术也很“硬核”——世界首次使用碳纤维复合材料制作奥运火炬外壳,采用氢气做火炬燃料,能耐-40℃的低温,在10级大风和暴雨下还能稳定燃烧,火炬外壳被800℃火焰灼烧也不变形不变色。“飞扬”火炬是怎样研制生产出来的呢?中国石化上海石化承担了北京冬奥会火炬研发和生产任务,南都记者专访了上海石化副总经理、火炬量产项目领导小组副组长黄翔宇,他讲述了“飞扬”火炬的诞生记。
1
火炬外形美观、科技先进、能源洁净
南都:“飞扬”火炬跟以往的奥运会火炬相比,有什么创新点和亮点?
黄翔宇:首先是外形上的亮点。相比于2008年北京奥运会的火炬,“飞扬”火炬外形更飘逸,造型如两条丝带飞扬飘舞,这代表了我们奔向第二个百年奋斗目标的昂扬奋进的精神风貌,给人的感觉非常好。
第二个亮点是火炬的科技感。“飞扬”火炬使用碳纤维复合材料制作外壳,使其具备“轻”“固”“美”的优点。往届奥运会的火炬,外壳一般都是用金属做的,例如钢、铝合金等,非金属材料几乎没有使用过。而我们这次使用碳纤维复合材料制作火炬外壳,是奥运史上的第一次。碳纤维具有很多优点,它的相对密度不到钢的1/4,抗拉强度却是钢的7-9倍,是一种高端的复合材料。
第三个亮点是使用清洁能源氢气做火炬燃料。往届的奥运火炬一般采用丙烷、丁烷做火炬燃料,丙烷和丁烷都是温室气体,燃烧会产生二氧化碳,不够清洁环保。而这次我们使用的氢气取自于水,燃烧后又变成水,实现了零碳排放,这与北京冬奥会的绿色办奥的理念以及双碳目标都是契合的。
2
我突发奇想提出碳纤维可应用在火炬外壳上
南都:上海石化是怎么接到冬奥火炬研发任务的?
黄翔宇:上海石化接到火炬的研发任务是源自对体育界朋友的一次接待。2019年9月,上海石化接待了几个体育界的新客户。在给客户介绍碳纤维技术时,我们讲到碳纤维可以用在高尔夫球杆、网球拍等体育器材上,这时候客户对我说,他们参与过2008年北京奥运会火炬的研制工作,现在正在考虑研制冬奥火炬的事情,当时我就突发奇想,提出碳纤维可以应用在火炬外壳上。客户一听,觉得这是一个好主意,就把这个主意介绍给了冬奥组委。
大概在2020年6月,冬奥组委让上海石化用碳纤维复合材料做一个火炬样品出来。上海石化按照2008年北京奥运会火炬的外壳形状,做了碳纤维复合材料外壳样品拿去给冬奥组委看。
冬奥组委看过样品后,发现用碳纤维制作的火炬外壳很轻,而且强度很高,摔不坏,一下就喜欢上这个创意,决定把碳纤维放到冬奥火炬里。就这样,我们接到了冬奥火炬的研制任务,并且组建了一个技术攻关团队,我担任团队技术负责人。
3
边调整工艺边设计沟通研发总共用了9个月
南都:火炬研发过程中都遇到了什么困难?怎么解决的?
黄翔宇:2020年10月,火炬外壳设计出来后,我去冬奥组委发布会,亲手摸了设计样品,看到细节后第一感觉是,研制冬奥火炬对我们来说不容易,难点不少。
首先是,树脂的选择和加工的难题。“飞扬”火炬跟以往的火炬不同,它的外壳上半部分与火焰充分接触,要经过800℃火焰的灼烧。而我们的火炬外壳是碳纤维+树脂复合材料制作的,从我过去的经验来讲,没有哪款树脂经得起这么高温的灼烧。
为此,我们找了各种各样的树脂材料,最后终于找到了一款耐高温、耐火的树脂。就在我们以为问题基本解决的时候,又遇到了树脂固化成型的问题——这款树脂虽然耐高温,但是很黏,不好固化成型,我们与相关研发机构组建了联合团队,进行技术攻关,最后使树脂能够固化。
解决这个问题后,我们发现树脂固化后又出现了裂缝,经过分析发现,树脂出现裂缝是因为固化过程中的工艺出了问题,我们又自己摸索,最后一步步把这个问题解决掉了。所以火炬制作过程中材料的选择、成型工艺的确定都是有难度的。
其次,是与设计团队沟通的问题。“飞扬”火炬非常漂亮,是一个工艺品,但要想在研发过程中高度还原火炬设计样品的美观度是很有挑战性的。在制样的过程中,设计团队精益求精地不断修改设计,研发单位就根据设计单位的修改意见不断地调整模具,压力很大。
后来,我们邀请设计师来到我们研发单位现场沟通交流,明确哪些设计能实现、哪些不能实现,经过几个月的反复协调,最后得到了一个大家都满意的产品。所以是一边调整工艺,一边跟设计团队沟通,才最终研制出火炬外壳。
2021年3月17日,我们研发的火炬通过了点火测试,冬奥组委对我们研制的火炬外壳非常满意,认为能达到他们的要求。从2020年6月接到任务,到最终研制出来,“飞扬”火炬外壳的研发总共用了9个月的时间。
4
从研发到量产要保证火炬各个零部件无偏差
南都:“飞扬”火炬从研发到量产有什么不同?量产过程需要注意什么?
黄翔宇:做一个东西和做一批东西是不同的,做一个东西可以反复打磨,做到极致,但是做一批东西,就需要制作工艺稳定可靠,可重复性要好,生产出来的每一个火炬都得确保一样,这对过程质量的把控、验收标准和各个零部件之间的配合的要求都是非常高的。我们最初以为只需要研发火炬外壳,不知道还要承担量产的任务。后来冬奥组委把量产的任务也交给了我们,接到量产任务之初,我们的压力是非常大的。
为了让火炬的内外飘带、氢气瓶、减压阀等各个零部件组装起来没有偏差,我们把每一道工序的制作工艺全部书面写了出来,而且经过了多次审核,并且派人到火炬生产的每个环节的现场把控质量,对每个细节都要检测,保证火炬的各部件不能有任何偏差。我相信,火炬的量产经历提升了火炬产业链上每一家参与企业的实力,让我们每家企业将来都更有信心接类似的任务,这是我们这次做火炬最大的收获。
南都:您深度参与了这次冬奥火炬的研制和量产过程,心情如何?
黄翔宇:作为这次冬奥火炬量产项目领导小组的副组长、技术负责人,我的心情还是很激动的。非常感谢冬奥组委对我们的信任,研发生产冬奥火炬对我们来说是一次不可复制的经历,这很值得骄傲。冬奥火炬马上就开始传递了,我们有压力,但也更有信心。
2月2日火炬开始传递的时候,我肯定会在电视前收看直播,每一把火炬都是经过我们的手做出来的,每一棒火炬的传递我们都非常关注。
采写:南都见习记者 丁境炫